1. The main cause of tapping and tooth decay
In the daily tapping, the main reasons for the tapping and toothing of the tap are summarized as follows: 1 In the case of reversal, the high point of the cutting root squeezes the cutting edge and is called "disintegration". 2 When reversing, the cutting debris is squeezed between the tap and the workpiece to squeeze out the cutting edge. 3 Because the material of the workpiece is too sticky, if the lubrication is not good, the cutting edge will be glued off, which is called “crackingâ€. 4 Because the workpiece material is too hard, the top of the tooth is removed, which is called "tooth". 5 When the workpiece has sand holes and uneven material, the top of the tooth will be removed, which is called “toothingâ€. 6 Collisions caused by unreasonable operation, such as fast cutting speed, collision of the head and the like, the resulting teeth are called "toothing".
The reason 1 is that most people do not realize the seriousness of their destructive ability. For example, Tiannuo CNC Machinery Co., Ltd., an internship factory of Weihai Vocational and Technical College, produces a CNC toolholder with a wire hole at the end of the cutter bar. They are: Model 40 series corresponding to M16, Model 45 series corresponding to M20, Model 50 series. Corresponding to M24, there is a problem that the tap life is not long, and most of it is scrapped due to broken teeth. This problem is also common among other brothers, even in the national machinery manufacturing industry. Because this problem exists in manual tapping, ordinary machine tool tapping, and CNC machine tool tapping, the damage to the tap is extremely great and should be taken seriously by everyone. The following analyzes the causes and countermeasures of the problem.
2. Solution
First, the description is made as shown in Fig. 1. In Fig. 1, the workpiece is fixed, the tap is rotated, the main cutting edge is marked E, and the back chip is marked F. Figure 1a is the tap cutting, the tap is reversed, the cutting is broken to facilitate the discharge; Figure 1c is the tap back chip removing edge F, cutting the cutting, leaving the high point G, the height is the tap back angle difference (EF arc length The back angular difference height); Figure 1d is the tap collapse due to the high point G.
figure 1
For most materials, when the backing chip F is retracted to the vicinity of the cutting root, the cutting can be broken (see Figure 1b), but there will be a high point. If you continue to retreat, use the backing blade F to set the high point. Shovel short or cut off the cutting (see Figure 1c), and then continue to retreat, is the forced retreat of the interference, because the tap is behind the slope with a 6 ° ~ 8 ° back angle, the maximum interference near the main cutting edge E, The most easy over-extrusion squeezes the main cutting edge to collapse (see Figure 1d). The current machine tap cutting edge is short, mainly cutting with two buckles and half wire, especially the larger diameter tap, the single-blade cutting margin is large, the workpiece material encountered is slightly sticky, and the resistance of the high point G increases. Large, at this time, the tap is most likely to collapse, because the top resistance of this high point and the force during cutting, the cutting edge is alternating fatigue of the two-way fatigue, greatly reducing the endurance limit of the tap blade, as shown in Figure 2 Cut the M12 tap (no tapping), reverse the photo of the main cutting edge too high. The raised portion is the high point G. After the main cutting edge is too high, there is obvious trace of friction and brightening at the high point, but the protrusion is still very obvious, and it is easy to cause the tap to collapse.
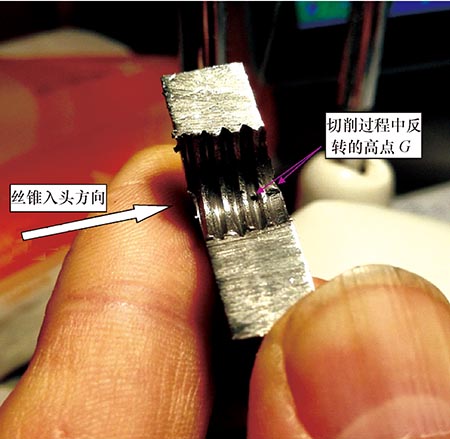
figure 2
Through a lot of practical operations, it is found that when the tap reversal is less than one-third of the cutting edge, that is, the three-blade tap reversal is less than 1/3, and the four-blade tap reversal is less than 1/4, the probability of tap collapse is reduced to The lowest, as long as the tap is reversed, the cutting is broken, and the chip removal is easy, so that the purpose of retreating can be achieved, and the main cutting edge does not have to pass the high point G, which can effectively prevent the tap from collapsing due to the high point G extrusion. Especially for manual operation, the main cutting edge is not too high, so it is easy to achieve the purpose, and it is not easy to break the tap. When maneuvering the thread, the fitter or the lathe should control the retraction stroke as much as possible, and try to avoid the main cutting edge from retreating to the high point, which can greatly improve the life of the tap. For example, we have not controlled the retracting stroke before, and attacked the M12 thread on the Z512 drill (production of about 150 pieces of F214 boring head slider, each piece of M12 thread, thread depth of 18mm, through hole, material 40G) generally needs 2 More than 6 taps have been used for the above taps. Since the high point is considered to be harmful to the tap, try to control the retracting stroke and try not to let the main cutting edge pass the high point G (foot switch control) for two consecutive months. Three batches were produced (105 in the first batch, 105 in the second batch, and 103 in the third batch). As a result, the life of the tap was greatly improved, with the first batch using 2 taps and the second batch using only 1 (due to no Disintegration, when the production exceeds the 70th, gently grind the front of the tap blade.) The third batch used 2 taps, but the first tap was 81 pieces and the second tap was only 22 pieces. This process The tap is intact.
As for the CNC machine tool, because the program is fixed, the ordinary operator can not change the program, so this problem cannot be solved. Here, it is recommended to the CNC machine manufacturer to adjust the CNC machine program so that the machine operator can set the rotation of the tap before and after. When maneuvering the thread, try to control the retraction stroke as much as possible, and try to avoid the main cutting edge from retreating to the high point, which can greatly improve the life of the tap. Through investigation and research, it is found that most of the damage of the tapping of the CNC machine tool to the tap is the disintegration. If it is not broken, it can be simply bluntly trimmed to the front end of the tap, so that it can be used sharply. If the tooth is broken, it is not worth repairing.
3. Conclusion
The reason why the above problems have not been paid attention to in the past is because the book generally tells us that after every certain amount of advancement of the tap, it is inverted by 1/4 to 1/2, so that the cutting is broken and it is easy to discharge. By looking at some books, it is found that the description of the tapping thread belongs to this statement. Therefore, through practice, the proposed teaching materials should be changed according to the actual situation: the four-blade tap should be inverted less than 1/4, and the three-blade tap should be inverted less than 1/3, so that the cutting is broken and easy to discharge. Therefore, the mechanical colleagues should go to the factory with more taps to understand the reasons for the excessive damage of the tap when the CNC machine tool taps, and strive to adjust the existing technology, improve the service life of the tap, and contribute to the conservation-oriented society.
references:
[1] Yan Ping. Fitter Technology [M]. Beijing: Mechanical Industry Press, 1979.
[2] Office of the Textbook of the Ministry of Labor and Social Security. Fitter craft and skill training [M]. Beijing: China Labor and Social Security Press, 2001.
Shandong Fiberglass Group Corp. is a state owned enterprise with registered capital RMB400million, covering an area of 800,000sqm. It has 3 subsidiaries: Tianju Energy Saving Material Corp, Glasstex Fiberglass Material Corp and Yishui Thermo Electricty Plant. Currently we can provide 7 categories products with 300 more kind products in ECR fiber, Ecering@Tex Modified Fiber,c-glass fiber, Wallcoveing, Insect Screen, PCB Tissue and Mesh.We are certified enterprise group with IS09001, ISO18001, ISO14001, Germannischer Lloyd(GL),UL and CQM certificates. Now we ranked China 4th largest Fiberglass producer. In 2020, we would become world Top 7 largest fiberglass producer with roving annual capacity 450,000tons, and fabrics capacity 230,000,000sqm. And some of our products capacity would become China Top 1, like C-CR Speicial glass fiber, ECR High properties glass fiber, Ecering@-Tex modified glass fiber and wallcovering.
Roving For Pultrusion
Roving For Pultrusion,Low Fuzz Fiberglass,Direct Supply For Fiberglass,Direct Roving For Pultrusion
Shandong Fiberglass Group Corp. , https://www.en-glasstex.com