The typical operational steps for a control valve usually involve several stages: operation, backwash, salt absorption, slow rinse, replenishing the salt chambers, and periodic cleaning. These processes can be summarized into five main stages: operation (also known as water production), backwashing, salt absorption (or regeneration), slow rinsing (displacement), and rapid rinsing. While the core steps remain quite similar across various water softening systems, minor differences might arise due to specific operational requirements or additional processes. Most water softeners relying on sodium ion exchange are fundamentally based on these five stages, where the amount of salt used plays a crucial role.
During the slow rinse (displacement) phase, after the resin has been treated with brine, it is rinsed slowly using untreated water at the same flow rate to eliminate any remaining salt. During this step, the functional groups that have exchanged sodium ions still retain significant amounts of calcium and magnesium ions. Based on practical experience, this stage is considered critical for effective regeneration, leading many to refer to it as the displacement process. Typically, this phase lasts around 30 minutes, matching the duration of the salt absorption process.
The rapid rinse follows next, aiming to thoroughly wash away any residual salt. This is achieved by rinsing the resin with raw water at a flow rate similar to normal operating conditions. The final output of this process is typically directed towards fully automated softening systems, which often incorporate an additional brine injection step.
Backwashing occurs after the system has been in operation for a while, accumulating debris from the incoming water above the resin layer. To ensure optimal regeneration, this accumulated dirt needs to be removed, exposing the resin completely. During backwashing, water enters from the bottom of the resin bed and exits from the top, flushing out the trapped debris. This process usually takes between 5 to 15 minutes.
Salt absorption (regeneration) involves introducing brine into the resin tank. Traditional setups use a salt pump for this purpose, whereas modern automated systems employ specialized injectors to draw in brine as long as there’s sufficient water pressure at the inlet. In practice, regenerating the resin with brine flowing through it at a controlled, slower pace yields better results than simply immersing the resin in brine. As such, most water softening systems regenerate the resin by allowing brine to flow through it gradually. This process generally takes around 30 minutes, with the subsequent rapid rinse lasting approximately 5 to 15 minutes.
High Speed Heavy-duty Pallet Handling Forklift
High-speed heavy-duty pallet handling forklifts are classified based on various factors, including their load capacity, lifting height, mast type, and drive system. Understanding these classifications is crucial in selecting the right forklift for specific applications and ensuring optimal performance and efficiency.
Load Capacity:
High-speed heavy-duty forklifts are categorized based on their maximum load capacity, which is typically measured in tons. The load capacity determines the maximum weight of the pallet and its contents that the forklift can safely lift and transport. Higher load capacities are required for handling heavier materials and larger pallets.
Lifting Height:
The lifting height of a forklift refers to the maximum height it can reach when lifting a load. Forklifts with higher lifting heights are necessary for storing materials at elevated levels in warehouses or for loading and unloading containers.
Mast Type:
Forklifts can have different mast types, including:
Simplex Mast: A simplex mast has a single vertical column that can be raised and lowered.
Duplex Mast: A duplex mast has two vertical columns, allowing for greater lifting heights and stability.
Triplex Mast: A triplex mast has three vertical columns, providing even higher lifting capabilities and improved stability.
Drive System:
Forklifts can be powered by different drive systems. These forklifts are equipped with powerful engines, heavy-duty frames, and advanced hydraulic systems to handle demanding applications in warehouses, distribution centers, and manufacturing facilities. They are essential for industries that rely on efficient material handling, such as logistics, manufacturing, and retail.
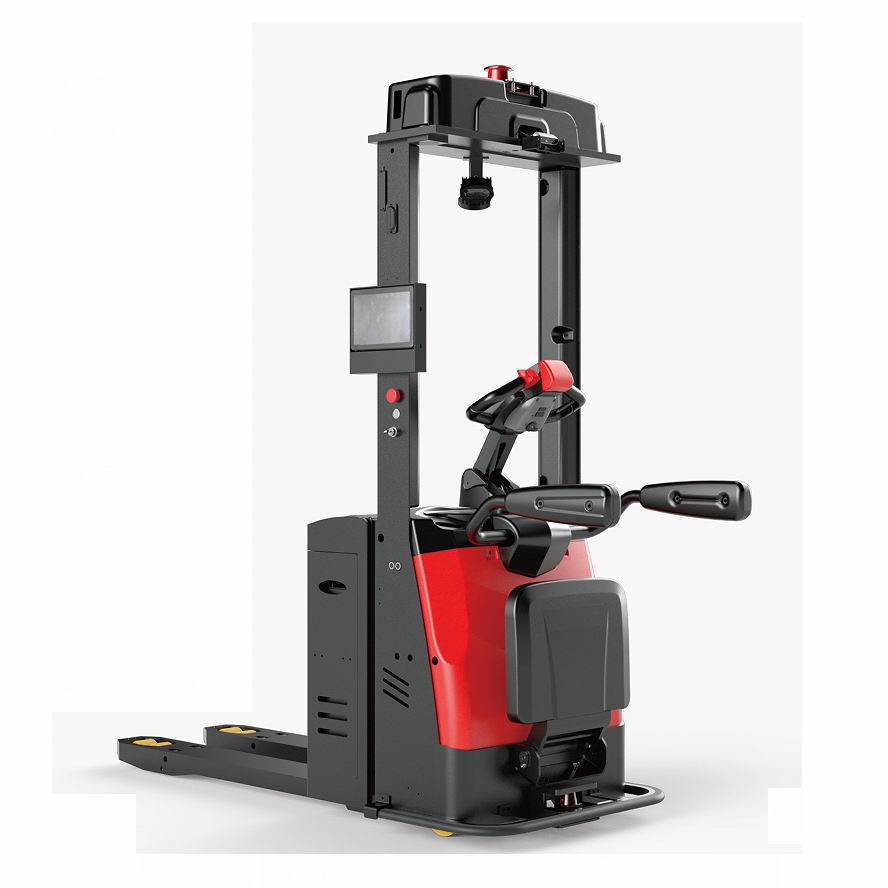
Internal Combustion Engine (ICE): ICE forklifts are powered by diesel or gasoline engines and are suitable for outdoor applications and heavy-duty tasks.
Electric Forklifts: Electric forklifts are powered by batteries and are ideal for indoor applications where noise and emissions are a concern.
Other Considerations:
In addition to the above factors, other considerations when classifying high-speed heavy-duty pallet handling forklifts include:
Tire Type: Forklifts can have pneumatic, solid, or cushion tires, each with its own advantages and disadvantages.
Steering Type: Forklifts can have mechanical or hydraulic steering.
Safety Features: Safety features such as seat belts, alarms, and backup cameras are essential for operator safety.
By understanding these classifications and factors, you can select the most appropriate high-speed heavy-duty pallet handling forklift for your specific needs and ensure efficient and safe material handling operations.
allet handling, material handling, warehouse equipment
Jiangsu Xicang Intelligent Technology Co., Ltd. , https://www.xciwarehousing.com