The purpose of the pump trip fault test is to identify the root cause behind the pump tripping phenomenon and to monitor the behavior of the meters during the switch closing process in order to determine what triggered the trip. During the test, the voltmeter is used to monitor the microcomputer trip circuit, the milliammeter tracks the operation of the differential relays 1CJ and 2CJ, and the ammeter monitors the thermal protection loop. After connecting the meters, the feed pump is started. After a period of testing, the pump trips once, and the milliammeter needle deflects, while the other meters remain unaffected. At the same time, the new XJL-0025/31 integrated block signal relay 1XJ also activates, confirming that the trip was caused by the differential protection action.
Root Cause Analysis
The first assumption when the differential protection operates is that there might be an internal fault within the protected device. Through routine inspection, the motor and its cable were found to be in good condition, and the differential relay was verified to be functioning properly. Additionally, the polarity of the current transformers was confirmed to be correct. After eliminating potential equipment failures and wiring errors, it became clear that the differential protection activated during the motor's start-up phase, indicating that the differential current exceeded the relay's set value at that moment.
There are two main reasons for the differential current under normal conditions: First, the current transformers on both sides of the motor may have different ratio errors, resulting in a small difference current that is less than 5% of the motor’s rated current. Second, differences in the secondary load of the current transformers on either end can also lead to variations in their ratios, causing a difference current. In this case, the difference in the secondary load of the current transformers in the differential protection circuit was due to the length of the secondary cables, which was about 50 meters. The power consumption of the differential relay at rated current was not more than 3 VA, so the secondary load was not heavy. The current transformers used for differential protection on the feed pump motor (model LMZBJ-10, B-class, 15 times rated current, 600/5 ratio, 40 VA capacity) fully met the required secondary load specifications.
However, the situation changes during motor startup, when the current is significantly higher. At this point, the current transformers on both ends may become saturated. This can lead to large secondary differential currents due to inconsistent magnetization characteristics between the transformers.
According to the settings of the LCD-12 differential relay from Acheng Relay Factory, the operating current setting is calculated as Izd = △I1 × Kk × In / N = 0.06 × 3 × 356 / 120 = 0.534 A, where △I1 is the maximum error of the tail current transformer during normal operation (0.04–0.06), Kk is the reliability coefficient (2–3), In is the motor's rated current, and N is the current transformer ratio. It should be set at 1.0 A. When using B-class current transformers, the operating current is set at 1.5 A with a braking coefficient of 0.4. However, the differential protection may occasionally activate during motor startup because the B-class current transformers have a lower saturation point and lower saturation resistance, which cannot meet the requirements of the differential relay.
Typically, D-class current transformers are recommended for differential protection circuits, as they have a higher saturation point, making them less prone to saturation and reducing the differential current during motor startup. Replacing the B-class current transformers with D-class ones and setting the differential relay’s operating current at 1.0 A with a braking coefficient of 0.4 eliminated the issue of the switch tripping during closure.
PTFE packing is made from raw material belts and is suitable for sealing valves, kettles, and pumps in corrosive environments within industries such as chemical, pharmaceutical, food, petrochemical, and power.
Technical Parameters:
Temperature: -200°C to 280°C
Line Speed: 20 m/s
Pressure: 2 MPa – 15 MPa
Chemical Resistance: pH 0–13
Aramid packing is designed for granular fluids, steam, organic solvents, acids, alkalis, and similar media, commonly used in sealing applications for machinery, pumps, valves, pipes, and containers in fluid conveyance systems.
Features: Excellent lubricity and wear resistance, high strength, high grinding capacity, good chemical resistance, high rebound, low cold flow, and easy disassembly. Ideal for dynamic sealing in media containing solid particles.
Technical Parameters:
Temperature: -100°C to +300°C
Pressure: 35 MPa
Chemical Resistance: pH 2–13
Hebei Innovation Sealing Material Co., Ltd. specializes in a wide range of sealing products, including graphite, asbestos, PTFE, ceramic fiber, glass fiber, aramid, rubber, PTFE sheets, metal winding mats, ladle pads, copper pads, octagonal gaskets, various types of packing, and gaskets.
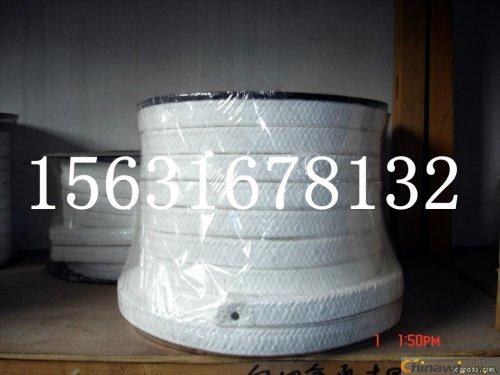
Round Mixer
Good quality round concealed bath shower mixer with diverter
PRODUCT INFORMATION
|
Name
|
concealed bath shower mixer
|
Brand name
|
HP
|
Feature:
|
Hot cold control
|
Material:
|
Brass body(Cu >=59%), Zinc(or brass) handle, Brass assembly fitting
|
Plating:
|
Chrome plate
|
Installation:
|
In-wall
|
Water Pressure Testing:
|
1-1.3MPA
|
Oem:
|
Yes
|
Cartridge Life time:
|
500,000 cycles
|
Guarantee time:
|
5 years.
|
Round Mixer,Round Pin Sink Mixer,Round Mixer Tap Connector,Stainless Steel Round Mixer
KaiPing HuiPu Shower Metalwork Industrial CO,LTD , https://www.hp-shower.com