Analysis and Elimination of Water Leakage Faults in Submersible Pumps
Before using a submersible pump, it is essential to perform a thorough inspection of the cable, switch, and electric shock protector. Ensure that all electrical components are functioning properly, the cable is undamaged, and pay special attention to identifying the yellow and green two-color wires, which are grounded to prevent electric shocks. It is recommended to check the insulation resistance of the submersible pump before each use. The resistance should be at least 0.5 MΩ. If it falls below this level, the pump should be dried thoroughly before operation. Regularly inspect the drain hole and vent hole of the submersible pump. If there are no signs of damage, tighten them as needed. When lowering or lifting the submersible pump into or out of water, always disconnect the power supply first. Then, pull the rope attached to the lifting ring, ensuring that the cable is not pulled directly. Avoid burying the submersible pump in river mud. If the water contains a lot of debris, place the pump inside a basket or mesh container before submerging it. This helps protect the pump from damage. After operating the submersible pump for 300 hours, conduct a sensitive water test. If the amount of water or oil-water mixture discharged is less than 25 mL, the pump can continue to be used. Otherwise, check the seal and rubber ring for damage. When testing the submersible pump outside of water—such as checking its direction—it must not exceed 5 minutes to avoid overheating and damaging the motor. Submersible Pump Water Leakage Faults Most leakage issues in submersible pumps are caused by aging or wear of the sealing components. In addition to replacing seals, several simple repair methods can be applied. For example, if the rubber seal in the nylon seat is worn, remove it and replace it with a new one. If the fastening spring has lost elasticity or broken, replace it with a wire of suitable diameter. If the seal ring loses its elasticity due to long-term use, remove it and cut a piece of paper or cloth (about 0.3–0.5 mm thick) to fit the groove slightly larger than the original. Reinstall the original seal. If the first seal is severely worn, remove the nylon ring and wrap asbestos rope coated with grease around the stainless steel sleeve, filling it slightly higher than the original. Then, apply more grease and tighten the nylon seat with bolts. In cases where the seal box and cast iron seal ring lose their elasticity, remove the seal ring and insert a cardboard pad (6–1 mm thick) into the groove. Place the seal back in position. If the rubber seal in the oil hole is damaged, use a piece of tape, cut to a size slightly larger than the bolt, add a flat washer, and install it in the oil hole. Aramid Packing Application: Suitable for sealing granular fluids, steam, organic solvents, acids, alkalis, and other media in machinery, pumps, valves, pipes, and containers used in fluid conveyance systems. Features: Excellent lubricity, wear resistance, high strength, good chemical resistance, high resilience, and easy disassembly. Ideal for dynamic sealing in media containing solid particles. Technical Parameters: Temperature range: -100°C to +300°C; Pressure: 35MPa; Chemical resistance: pH 2–13. Graphite Packing Adaptability: Used for sealing hot water, high-temperature steam, heat exchange media, hydrogen, ammonia, hydrocarbons, cryogenic liquids, etc. Suitable for petroleum, power plants, chemical, and steel industries. Features: High mechanical strength, flexibility, and protection for the shaft. Offers superior sealing performance in combination with other packing materials. Effective for high-temperature and high-pressure sealing. Technical Parameters: Temperature: 800°C; Pressure: 35MPa; Chemical resistance: pH 0–14. PTFE Packing Application: Made from raw material belts, ideal for sealing valves, kettles, and pumps in corrosive environments within chemical, pharmaceutical, food, petrochemical, and power industries. Technical Parameters: Temperature: -200°C to 280°C; Line speed: 20 m/s; Pressure: 2–15 MPa; Chemical resistance: pH 0–13. Ceramic Fiber Packing Made from high-quality ceramic fiber, it offers excellent wear resistance and high-temperature performance. Widely used in high-temperature sealing applications such as steel mills and petrochemical plants. It can serve as an alternative to asbestos packing with excellent results. SUNWELL P803P – Dip PTFE Ceramic Fiber Packing: Impregnated with tetrafluoro emulsion, it provides low friction and enhanced structural strength. SUNWELL P803S – Metal Reinforced Ceramic Fiber Packing: Enhanced wear resistance and pressure resistance through the addition of metal fibers. SUNWELL P803R – Silicone Core Ceramic Fiber Packing: Improved resilience and tighter sealing with a silicone core. Outstanding Performance: 1. Low maintenance costs and easy control. 2. Strong structural integrity and high-temperature resistance. 3. Economical solution, suitable for areas where asbestos is restricted. Ceramic fiber packing is ideal for high-temperature and high-pressure equipment like pumps, valves, and machines. It is widely used in chemical, power, paper, food, and pharmaceutical industries for clean fluids, slurries, brines, emulsions, greases, hydrocarbons, solvents, and pulp. Technical Parameters: Pressure: 3–20 MPa Temperature: 800–1200°C pH Range: 3–14 Linear Speed: 12 m/s Hebei Innovation Sealing Material Co., Ltd. Mobile: [Phone Number] Phone: [Phone Number] Website: [Website URL] Contact: Business Manager
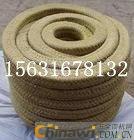
Shift fork normally applied in the transmissions, its function is help to slide gears into or out of engagement with other gears in order to change from one gear ratio to another in a manual transmission.
QFAP supply various kinds of shift forks to all over the world, main of our customers are digger/excavators manufacturers, lawn mower manufacturers, truck transmission factories and construction machinery companies.
Materials: carbon steel castings, stainless steel castings, alloys steel castings, aluminum die castings, forging steel castings, etc.
Surface treatment: painting, zinc plating, passivation, nickel plating, anodizing, polishing, etc.
Heat treatment: according to customer`s requirement.
QFAP have specialized in producing high precision Agriculture Parts more than 10years, Because of the long term cooperation, we could supply our customers not only the products but also our recommendation on the designs to saving costs.
Shift Fork,Shift Fork Gear,Transmission Shift Fork,Reverse Shift Fork
SHAOXING QIFENG AUTO PARTS CO., LTD. , https://www.sxqfap.com